Enhancing Your Productivity with High-Speed Spindles
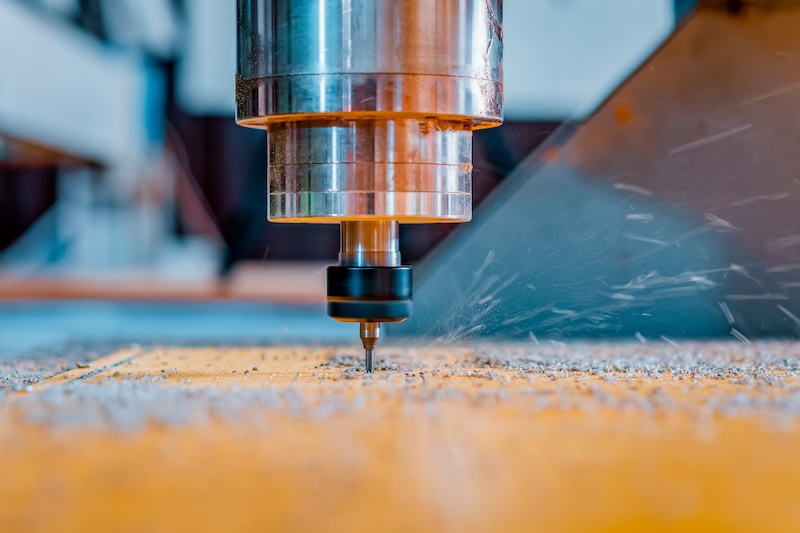
Success in any industry depends heavily on one key factor: productivity. For small businesses or large corporations, boosting productivity provides a competitive edge over competitors. One way to guarantee high-performance is by using a high performance machining spindle, a powerful tool built to deliver results.
What Are High-Speed Spindles?
In simple terms, a high-speed spindle is a precision tool driven by an AC motor, designed to achieve extremely high speeds. These advanced spindles offer significantly faster cutting capabilities compared to traditional models, making them ideal for applications requiring small-diameter cutters. Typical uses include micro-drilling, micro-milling, engraving, high-speed grinding, and the finishing of molds and dies, where both speed and precision are critical.
High performance spindles deliver greater speed, precision, and efficiency than traditional spindles. With higher material removal rates and improved accuracy, they boost productivity in machining processes. While standard milling and drilling typically operate at 20,000 to 50,000 RPM, high-speed spindles can achieve up to 250,000 RPM. These speeds enable faster cutting with greater precision and improved surface finishes. High-speed spindles also use lower torque than traditional spindles, relying on increased RPMs and smaller tools to generate cutting force.
Benefits of High-Speed Spindles
High-speed spindles have transformed manufacturing, boosting both efficiency and product quality. Here are some of the main benefits of using high-speed spindles in machining processes:
Faster Machining Times and Reduced Cycle Durations
Unlike traditional spindles with lower rotational speeds that require additional time to achieve precision, high-speed spindles facilitate faster, more efficient cutting and shaping of materials, optimizing the machining process.
The improved speed substantially reduces cycle times, allowing for faster production while maintaining quality standards. This advancement enhances productivity for manufacturers, leading to greater profitability.
Improved Surface Finish and Precision in Manufacturing
High-speed spindles significantly improve manufacturing processes by providing superior surface finishes and exceptional precision. Their advanced cutting and shaping capabilities enable materials to be machined with high accuracy, resulting in higher-quality parts and components.
Furthermore, high-speed milling spindles produce less heat compared to traditional options. This reduces the risk of material distortion or damage during machining, ensuring smoother finishes and more precise results.
Versatility in Machining Different Materials
High-speed spindles provide exceptional versatility, making them well-suited for machining a diverse range of materials. In contrast to traditional spindles, which can encounter difficulties with certain materials, high-speed spindles deliver precise performance across metals, plastics, and wood.
Higher Efficiency than Asynchronous Spindles
With their advanced engineering, high-speed spindles can reduce power consumption by 20% to 50% under comparable operating conditions. This ensures higher output per unit of energy, leading to enhanced efficiency and considerable cost savings.
Furthermore, their ability to operate at higher rotational speeds reduces wear and tear, resulting in an extended lifespan for equipment compared to conventional spindle motors. This increased durability translates to lower maintenance expenses and extended operational lifespans, thereby minimizing the need for frequent repairs or replacements.
Searching for high-performance spindles that deliver both versatility and efficiency? Reach out to us today!
Applications of High-Speed Spindles
High-speed spindles provide unparalleled speed and precision, establishing their essential role across various industries. This makes them particularly well-suited for applications across industries such as automotive, aerospace, and medical, where precise machining of diverse materials is essential:
- Aerospace: Aerospace components, such as turbine blades, engine parts, and airframe structures, require exceptional precision to ensure both safety and efficiency. High-speed machining, utilizing vertical machining centers (VMCs), has emerged as the preferred method for manufacturing these critical components due to its advanced accuracy and capabilities. This technology supports the production of complex geometries and tight tolerances, delivering aerospace components that consistently meet the industry’s stringent standards for quality and performance.
- Automotive: High-speed machining is essential in the automotive industry, particularly in the production of molds and dies used for processes such as injection molding and die casting. VMCs excel in achieving complex geometries with exceptional precision, making them a highly suitable choice for these components. Beyond ensuring precision, high-speed machining significantly enhances production speed, reduces costs, and optimizes processes within the automotive manufacturing process.
- Medical Manufacturing: High performance spindles are transforming the medical sector, especially in manufacturing hip and knee replacements. These procedures demand exceptional precision and ultra-smooth finishes for a perfect fit and optimal functionality. High-speed machining delivers the accuracy needed for these intricate components while enabling rapid prototyping and testing of new designs. By enabling researchers to produce complex, highly precise parts in substantially less time compared to traditional methods, high-speed machining is advancing both product development and patient care.
GMN’s Spindle Solutions
GMN USA delivers custom-engineered spindle solutions tailored to meet the specific needs of various industries and applications. Our precision-crafted spindles are built to exact customer specifications, ensuring exceptional performance for all machining tasks. Using advanced technology and high-quality materials, we produce spindles with superior reliability and accuracy, delivering optimal results for even the toughest operations.
Our portfolio includes a comprehensive range of spindles designed to address diverse speed and power requirements, including the highly adaptable SERIES UH line. This high-performance series offers exceptional solutions with spindle diameters spanning from 100 mm to 170 mm. With speeds of up to 120,000 rpm and power outputs ranging from 1.7 kW to 32 kW (S1), these spindles are specifically engineered to meet the demands in challenging machining applications.
Our spindle solutions feature advanced motor technology for precise speed and torque control, ensuring consistent performance. With an HSK interface designed to GMN standards, they offer seamless compatibility with a wide range of tooling systems.
Connect with a GMN USA expert today to discuss your needs and discover how we can help enhance and streamline your machining operations. Reach out now to get started!
Choosing the Right Spindle for Your Needs
Precision machining depends significantly on the selection of the appropriate spindle, a critical component for achieving superior results. Spindles play a vital role in the performance of equipment such as lathes, milling machines, and other industrial tools, as they enable the rotation of cutting tools at high speeds, directly influencing the accuracy and quality of the final output.
Advancements in technology and the increasing demand for enhanced productivity and precision have expanded the range of spindles available on the market. However, this variety can make identifying the optimal spindle for specific requirements a complex task. A comprehensive evaluation of operational needs and careful consideration of key factors can guide the selection of a custom-engineered spindle, ensuring optimal performance and unmatched precision.
Looking for a high-performance spindle to power your industrial equipment? GMN has you covered!
If you’re ready to take your performance to the next level, contact us today!